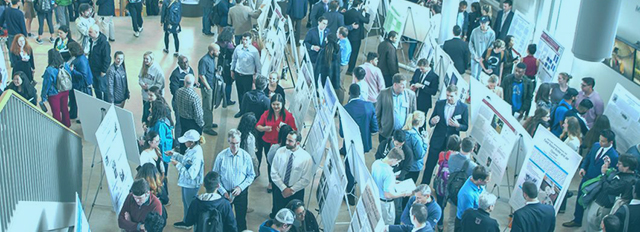
Posters and Papers
Event Title
Document Type
Open Access
Faculty Sponsor
Andrew Rapoff
Department
Mechanical Engineering
Start Date
22-5-2020 2:30 AM
Description
The Union College Rocket Team participates in the Spaceport America Cup along with 124 other teams around the globe. The Spaceport America Cup has multiple divisions of competition. The Rocket Team will participate in the 10,000ft commercial motor group. In this division, teams are required to send a rocket containing an 8.8lb scientific payload to an apogee of 10,000 feet using an off-the-shelf solid fuel motor. To receive full marks the rocket and payload must make a safe landing and have the proper equipment to be tracked and found. This year's rocket is named the Blazing Dutchie after the following modifications that have been done to the design from the previous year's Roaring Dutchman. To reduce packing size, as a way to minimize transportation and material costs, the body that houses the motor and parachutes has been decreased from 6in diameter to 4in. The section that houses the payload must have a 6in diameter to meet competition restraints on payload form factor. Therefore, a transition coupler of these two diameters is needed. As an initial choice the transition will be 3D printed out of ABS and consequent tests will determine the useability of this manufacturing method. The Blazing Dutchie is approximately 7.6 ft tall, will have dual chute deployment capabilities based on the real-time telemetry recorded by onboard flight computers. The decrease in weight and length of the new design calls for a lower power motor from last year's M-class. Using rocket simulation software we have decided on the Aerotech L-class 1325M solid fuel motor with a specific impulse of 4,700 N·s. he payload mentioned above will focus on monitoring atmospheric conditions as a way to track effects of climate change. It will be deployed from under the nose cone at ~4000ft consisting of a cylindrical 3D printed polymer lattice which will encase the payload electronics. A solid steel disc will be attached to the bottom of the lattice to ensure the payload falls in the correct orientation. The lattice will be hollow in the middle to allow a parachute 3 ft. in diameter to attach through the polymer lattice and to the steel cylinder. As the payload exits the rocket the parachute will deploy to allow for a slow descent and safe landing. Inside the walls of a polymer lattice, a Raspberry Pi Zero micro-computer will be connected to a SparkFun CCS811/BME280 Environmental Combo Breakout sensor. This sensor will read and log measurements of temperature, barometric pressure, humidity, TVOC and CO2 levels from the altitude that the payload is deployed to when it has reached the ground. To recover the payload and its valuable information, a Apogee Rockets, Simple GPS tracker, freq: 902-928 MHz, 17 dbm Spread Spectrum, will be used as it is one of the simplest all in one solution. In case of a signal loss the hand-held receiver will point towards the last known location.
Union College Rocket Team '20
The Union College Rocket Team participates in the Spaceport America Cup along with 124 other teams around the globe. The Spaceport America Cup has multiple divisions of competition. The Rocket Team will participate in the 10,000ft commercial motor group. In this division, teams are required to send a rocket containing an 8.8lb scientific payload to an apogee of 10,000 feet using an off-the-shelf solid fuel motor. To receive full marks the rocket and payload must make a safe landing and have the proper equipment to be tracked and found. This year's rocket is named the Blazing Dutchie after the following modifications that have been done to the design from the previous year's Roaring Dutchman. To reduce packing size, as a way to minimize transportation and material costs, the body that houses the motor and parachutes has been decreased from 6in diameter to 4in. The section that houses the payload must have a 6in diameter to meet competition restraints on payload form factor. Therefore, a transition coupler of these two diameters is needed. As an initial choice the transition will be 3D printed out of ABS and consequent tests will determine the useability of this manufacturing method. The Blazing Dutchie is approximately 7.6 ft tall, will have dual chute deployment capabilities based on the real-time telemetry recorded by onboard flight computers. The decrease in weight and length of the new design calls for a lower power motor from last year's M-class. Using rocket simulation software we have decided on the Aerotech L-class 1325M solid fuel motor with a specific impulse of 4,700 N·s. he payload mentioned above will focus on monitoring atmospheric conditions as a way to track effects of climate change. It will be deployed from under the nose cone at ~4000ft consisting of a cylindrical 3D printed polymer lattice which will encase the payload electronics. A solid steel disc will be attached to the bottom of the lattice to ensure the payload falls in the correct orientation. The lattice will be hollow in the middle to allow a parachute 3 ft. in diameter to attach through the polymer lattice and to the steel cylinder. As the payload exits the rocket the parachute will deploy to allow for a slow descent and safe landing. Inside the walls of a polymer lattice, a Raspberry Pi Zero micro-computer will be connected to a SparkFun CCS811/BME280 Environmental Combo Breakout sensor. This sensor will read and log measurements of temperature, barometric pressure, humidity, TVOC and CO2 levels from the altitude that the payload is deployed to when it has reached the ground. To recover the payload and its valuable information, a Apogee Rockets, Simple GPS tracker, freq: 902-928 MHz, 17 dbm Spread Spectrum, will be used as it is one of the simplest all in one solution. In case of a signal loss the hand-held receiver will point towards the last known location.